Discover how a successful Australian company merged three warehouses with the help of eBottli

Challenge: Centralising and Digitising a merge
Merging 3 different warehouses
Paper Centric Record Keeping
ERP system working in silo
Inheriting existing operational outdated process.
Stock and inventory management was done on paper, causing weekly stock-outs and bad deliveries due to human error.
Disconnection between the daily warehouse and administrative tasks made the processes very manual and time consuming.
Solution: eBottli's Stock & Inventory Tracking
eBottli designed an end-to-end customisable solution,
to optimise operations, organise localisation and improve operation traceability
Monitoring
Automated Process
Mobile solution
eBottli provided QR codes to promote accuracy indoors or outdoors. Resulting in exact location, movement, time & duration, history and stock control for business owner.
Digitizing warehouse operations with automated processes, and improved process analysis increased transparency and accountability. eBottli provided Business Process Management Notion (BPMN) to provide a standardized visual language for modeling business processes with clear and concise communication.
Mobile solution roll-out with ERP access and integration for Warehouse workers. Real-time traceability user experience with unique identifiers during manufacturing and up to dispatch.
Saved 2 hours a day
Checklist implementation
Dynamic Product Reporting
This has enabled us to save more than 2 hours a day and to have real-time access to stock quantities and their location.
Checklists help keep warehouse workers in check with day-to-day tasks, delegated work, and forward workload.
Make data-driven decisions through eBottli’s dynamic product reporting suite. Be prepared for upcoming audits to assist with sustainability and compliance with regulations.
Get in touch with our team today!
Learn from other customers success stories
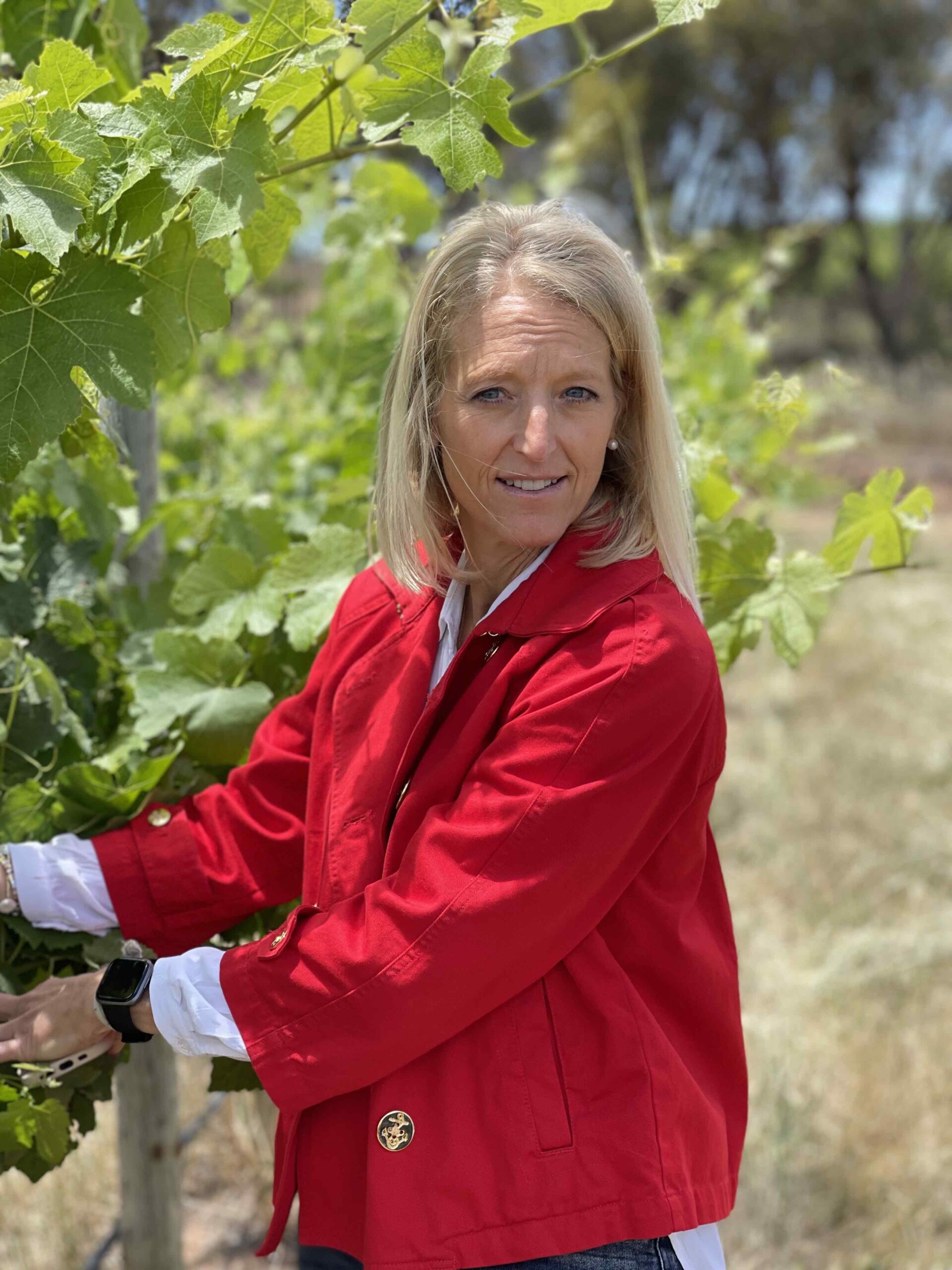
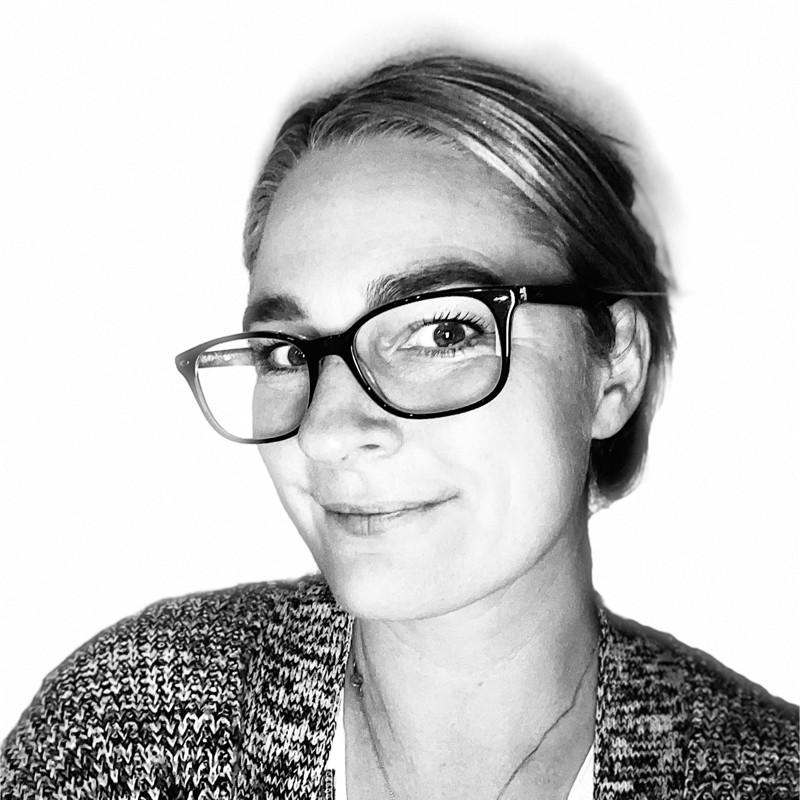
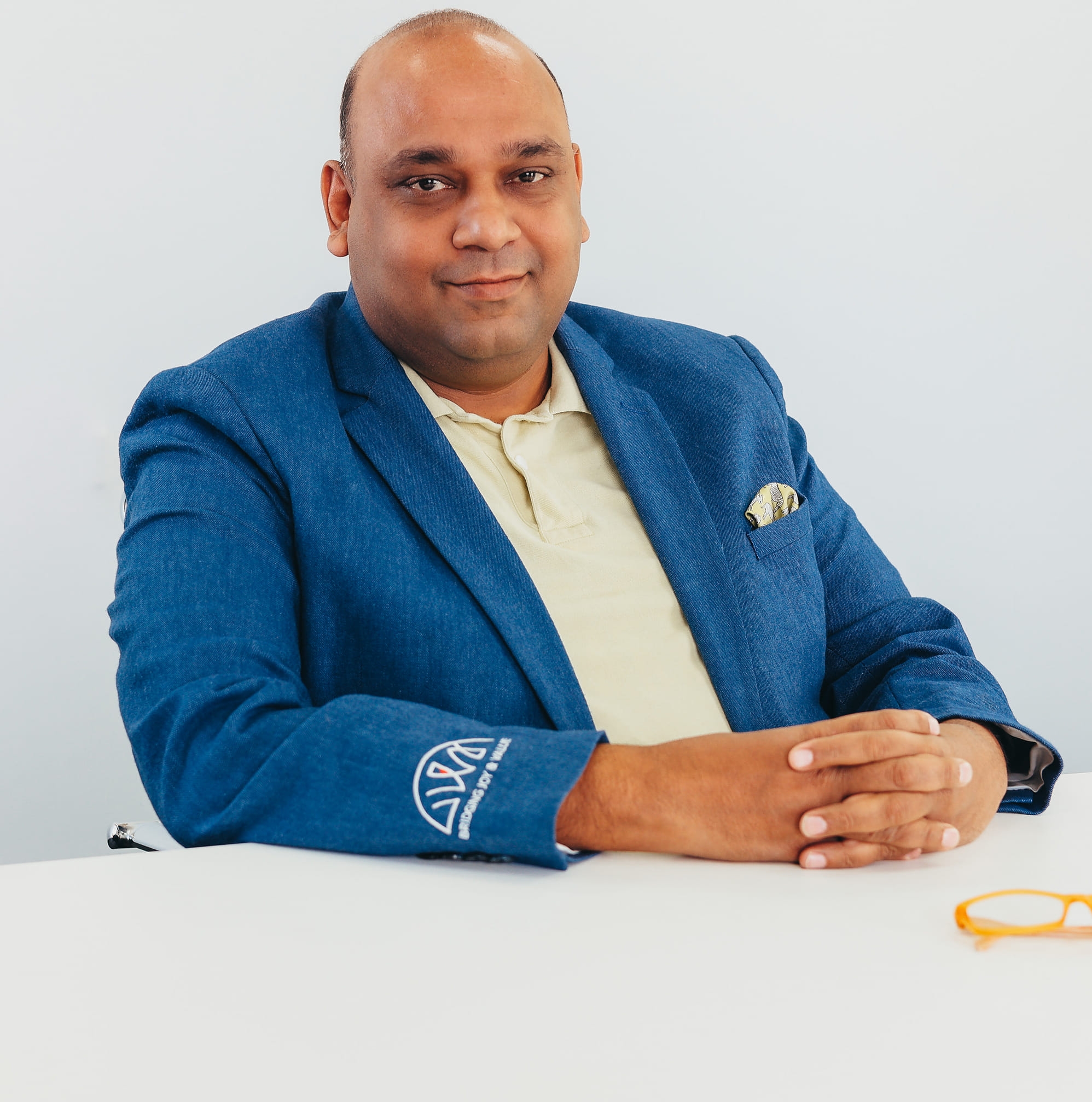
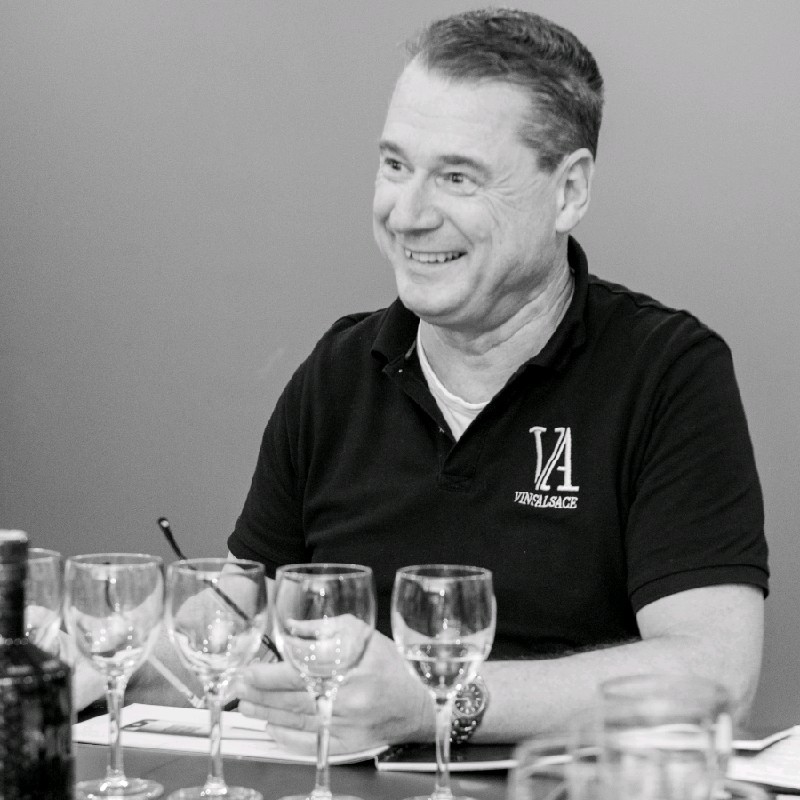
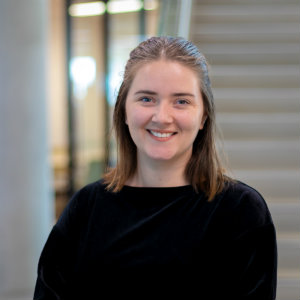